How to Choose the Right Rubber Material for Your Project
- Reliant Rubber
- Jul 16, 2024
- 3 min read
Updated: Jan 31
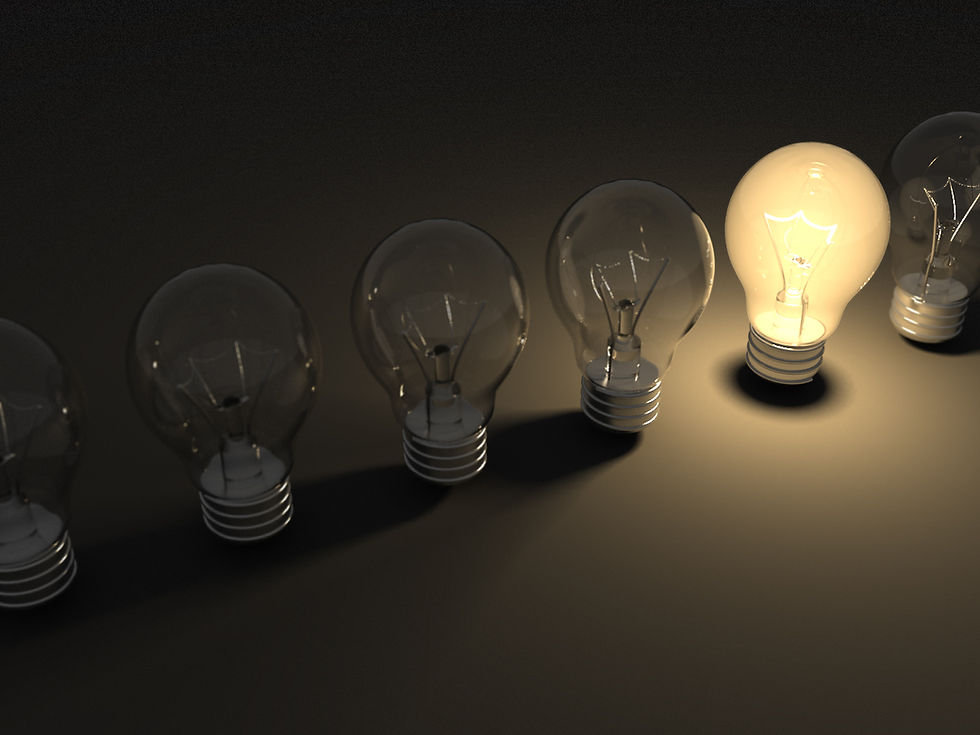
When starting a new project involving rubber materials, choosing the right type of rubber can be overwhelming. Many different types of rubber are available, each with unique properties and applications. Selecting the correct kind of rubber is essential for the success and durability of your project. This guide will help you understand the vital factors to consider and give you valuable insights into the most used rubber materials.
Understanding Your Project Requirements
Before diving into the specifics of rubber types, it's essential to have a clear understanding of your project requirements. Ask yourself the following questions:
What environment will the rubber be exposed to?
Temperature extremes
Chemicals
UV radiation
Ozone
What mechanical properties are necessary?
Tensile strength
Flexibility
Hardness
Abrasion resistance
Are there any specific industry standards or certifications required?
FDA compliance for food-related projects
ASTM standards for mechanical properties
ISO standards for quality management
Common Types of Rubber and Their Applications
1. Natural Rubber (NR)
Properties: High tensile strength, resilience, and abrasion resistance.
Applications: Tires, seals, gaskets, and vibration mounts.
Limitations: Poor resistance to ozone, UV, and chemicals.
2. Styrene-butadiene rubber (SBR)
Properties: Good abrasion resistance and ageing stability, cost-effective.
Applications: Tires, conveyor belts, and shoe soles.
Limitations: Moderate resistance to oil and chemicals.
3. Nitrile Rubber (NBR)
Properties: Excellent resistance to oils, fuels, and chemicals; good mechanical properties.
Applications: O-rings, fuel hoses, gaskets, and automotive applications.
Limitations: Poor ozone and weather resistance.
4. Ethylene Propylene Diene Monomer (EPDM)
Properties: Superior resistance to heat, ozone, UV, and weathering; good flexibility.
Applications: Automotive weather-stripping, roofing membranes, and garden hoses.
Limitations: Poor resistance to petroleum-based fluids.
5. Silicone Rubber
Properties: Excellent heat resistance, flexibility at low temperatures, and biocompatibility.
Applications: Medical devices, kitchenware, seals, and gaskets.
Limitations: Lower tensile strength and tear resistance compared to other rubbers.
6. Neoprene (CR)
Properties: Good chemical stability, flexibility, and moderate resistance to oil and weather.
Applications: Wet suits, industrial hoses, gaskets, and corrosion-resistant coatings.
Limitations: Moderate resistance to chemicals and lower resilience than natural rubber.
Critical Factors in Selecting the Right Rubber
Environmental Resistance
Temperature: Choose a rubber that can withstand the temperature range of your application.
Chemical Exposure: Consider the types of chemicals the rubber will be exposed to and select accordingly.
Weathering: For outdoor applications, ensure the rubber is resistant to UV, ozone, and weather conditions.
Mechanical Properties
Tensile Strength: Ensure the rubber can handle the required load and stress.
Flexibility: Depending on the application's need for flexibility or rigidity, select a rubber with appropriate elongation and hardness.
Abrasion Resistance: Choose a rubber with excellent abrasion resistance for high-wear applications.
Compliance and Certifications
Check for industry-specific standards the rubber must meet, such as FDA for food-related projects or ASTM for mechanical properties.
Final Tips
Consult with Suppliers: Contact rubber material suppliers for detailed information about their products' properties and best uses.
Prototype and Test: If possible, create prototypes using the chosen rubber material and conduct thorough testing to ensure it meets all your requirements.
Cost Considerations: Balance the cost of the material with its performance to ensure it fits within your project budget without compromising quality.
By carefully considering these factors and understanding the properties of different types of rubber, you can make an informed decision that will enhance the performance and durability of your project. Whether you're working on an industrial application, a consumer product, or a specialised device, a suitable rubber material is waiting to be discovered.
Comments